Introduction
At QOCO, we specialize in aviation maintenance software. Over the years, we’ve worked closely with airlines, OEMs, and MROs, and one thing has become crystal clear: disconnected systems can significantly hinder operations. This disconnect often results in increased manual processes, data silos, and compliance risks, which can ultimately disrupt operations.
But there’s a solution. By integrating MRO software with airline ERP platforms, airlines and MROs can unlock significant operational advantages. From improving predictive maintenance to enhancing inventory control and compliance tracking. This synchronization ensures seamless data flow, improving overall aviation maintenance management and delivering gains for MRO from digital solutions.
In this article, we explore the key benefits of integrating these two essential systems and how it can transform aviation maintenance management.
If you'd like to read more articles about MRO software, take a look at these:
For a more extensive insight on MRO Software be sure to read Everything you need to know about MRO Software, where we explore best practices, trends, and expert insights into MRO solutions.—a comprehensive guide on how MRO software enhances efficiency in aviation maintenance.
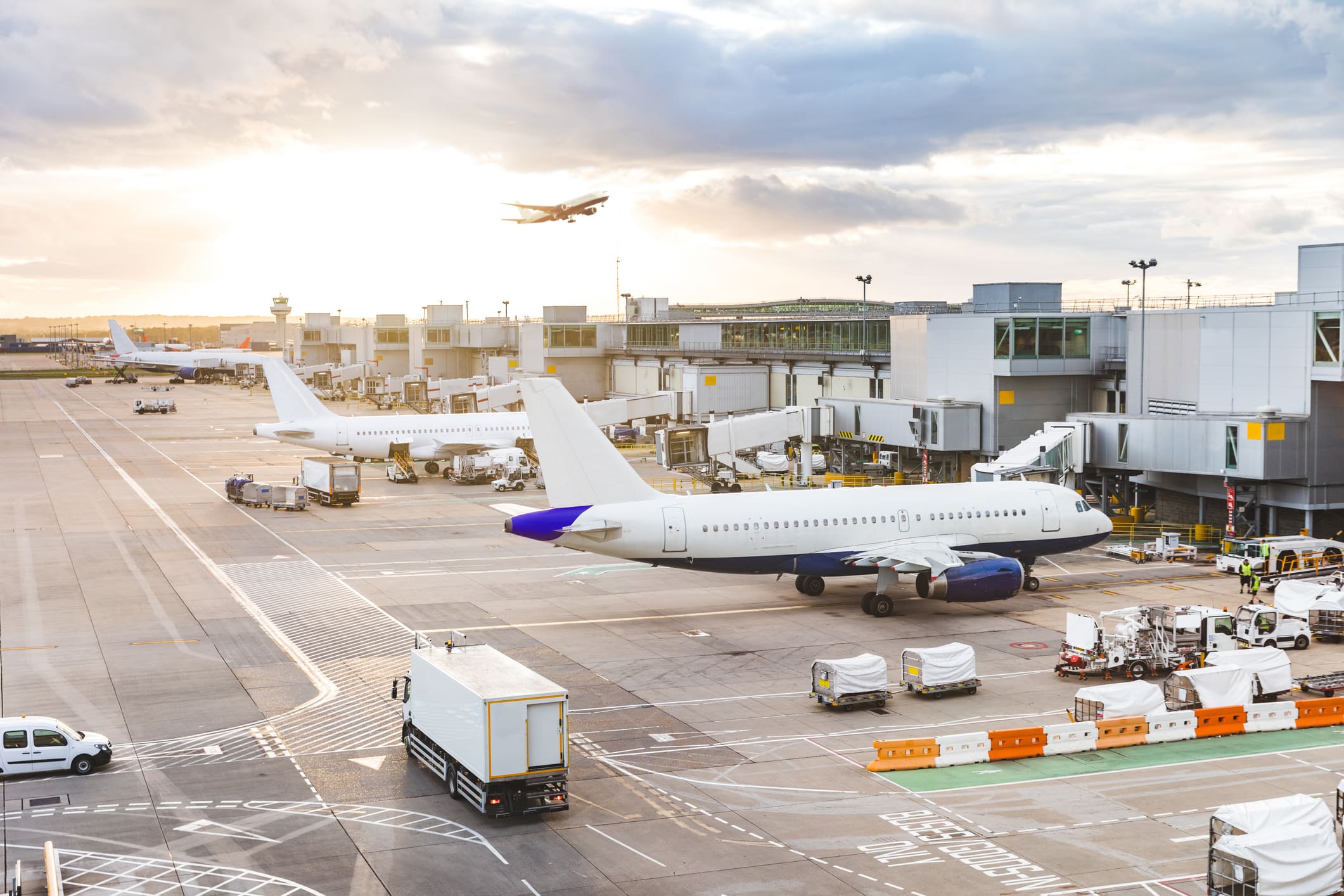
Why MRO and ERP Integration Matters in Aviation
The Role of MRO Software
MRO software is designed to manage the entire maintenance process—tracking work orders, managing spare parts, scheduling inspections, and ensuring compliance with aviation regulations. At QOCO, we’ve seen how manual processes can slow things down, which is why we developed MROTools, our advanced digital maintenance solution. It’s all about helping airlines and MROs work smarter, not harder.
The Role of ERP Platforms
On the other hand, airline ERP platforms are the command center for business operations—finance, HR, procurement, and fleet management. While ERP systems are powerful, they’re not built to handle the specialized demands of aircraft maintenance. That’s where MRO software comes in, filling the gap with real-time maintenance tracking, compliance reporting, and predictive analytics.
Here’s the important point: if these two systems are not connected, inefficiencies can arise. Maintenance teams have difficulty accessing the data they need, inventory mismatches become a source of frustration, and decision-making becomes reactive instead of proactive. Therefore, synchronization is crucial for addressing these challenges.
The Key Benefits of Synchronizing MRO Software with Airline ERP Platforms
-
Enhanced Operational Efficiency
Disconnected systems are like traffic jams—they slow everything down. When MRO software and ERP platforms work together, data flows seamlessly across departments. Manual input is reduced, errors are minimized, and maintenance workflows are automated. Thus, the aircraft can be serviced faster and returned to operation without unnecessary delays.
-
Optimized Predictive Maintenance
At QOCO, we’ve helped airlines implement predictive maintenance solutions that rely on real-time aircraft performance data. By integrating MRO software with ERP platforms, airlines gain AI-driven insights that predict component failures before they happen. This means fewer unplanned downtimes and fewer dreaded Aircraft on Ground (AOG) situations. According to a report by Aviation Week, LHT offers predictive maintenance via its Aviatar platform, which it says helps up to 30% of unscheduled removals.
-
Streamlined Compliance Tracking
Let’s face it—regulatory compliance is a headache, but it’s non-negotiable. With synchronized systems, compliance tracking becomes automated. Maintenance logs, part traceability, and service records are updated in real-time, making audits smoother and reducing the risk of costly penalties.
-
Improved Inventory Management
MRO operations require precise inventory control to avoid delays caused by missing parts. Inventory management optimization is a core benefit of system synchronization, ensuring that the right parts are available when and where they are needed—without unnecessary overstocking that ties up capital.
-
Better Fleet Management
Airlines need real-time visibility into aircraft status to plan flights and maintenance efficiently. When MRO software is integrated with ERP platforms, fleet managers can access real-time data on aircraft health, maintenance schedules, and serviceability, ensuring smoother operations and fewer disruptions.
-
Increased Software Interoperability
One of the biggest challenges airlines face is managing legacy IT systems that don’t communicate effectively. At QOCO, we understand the complexities of software interoperability and have developed solutions that seamlessly integrate MROTools with ERP platforms, eliminating data silos and making digital transformation easier.
Case Studies: How Airlines Benefit from MRO-ERP Synchronization
Success Stories from QOCO Clients
Many of our clients have seen substantial operational improvements after integrating MRO software with their ERP platforms.
- An international airline reduced maintenance-related delays by 20% after automating work order updates and inventory tracking.
- A leading MRO provider achieved a 15% reduction in spare parts procurement costs by synchronizing inventory data between their ERP and MRO solutions. Aircraft IT highlighted a similar case where an MRO achieved significant cost savings through system integration.
- A major airline improved compliance tracking, ensuring they were always audit-ready with up-to-date digital maintenance records.
Lessons Learned from Implementations
Through our years of experience, we’ve identified key factors that determine the success of MRO-ERP integration:
- Selecting flexible and scalable software solutions.
- Ensuring accurate data migration during the transition.
- Training maintenance and IT teams to adapt to new workflows.
Challenges and Considerations for Integration
-
Compatibility and Integration Barriers
Not all ERP and MRO solutions are built for seamless data exchange. That’s why at QOCO, we prioritize API-driven integration and custom-built connectors to ensure smooth interoperability.
-
Data Migration Complexity
Migrating data from legacy systems can be a challenge. McKinsey’s aerospace reports emphasize the importance of structured data migration for successful digital transformation,
The next three to five years will be pivotal for digital adoption While only 33 percent of respondents say digital is critically important to achieving their organizations’ priorities and objectives today, more than 70 percent say that it will be critically important within three to five years.
Airlines must ensure that historical maintenance records, inventory data, and compliance documents are properly structured before integration. Our team at QOCO has extensive experience guiding clients through this critical transition phase.
-
Managing Change in the Organization
Software integration affects multiple teams, requiring a well-planned change management strategy. Successful adoption depends on training staff, aligning stakeholders, and providing ongoing support—which we help facilitate through our tailored implementation services.
Conclusion: Future-Proof Your Maintenance Operations with QOCO
At QOCO Systems, we help airlines, MROs, and OEMs streamline maintenance operations through our digital solutions. Synchronizing MRO software with airline ERP platforms isn’t just a technical upgrade, it boosts efficiency, improves compliance, and reduces operational costs.
By leveraging our deep aviation expertise and advanced software solutions, we empower our clients to stay ahead in an industry that demands precision and agility.
Is your airline or MRO ready to integrate its systems and unlock new efficiencies? Contact us today to explore how QOCO can help you transform your maintenance operations.